Density | 8.9 g/cm³ |
Melting point | 1325-1370 °C |
Item | HC-276 | C-22 | C-4 | B2 | B3 | N |
C | ≤0.01 | ≤0.015 | ≤0.015 | ≤0.02 | ≤0.01 | 0.04-0.08 |
Mn | ≤1 | ≤0.5 | ≤1 | ≤1 | ≤3 | ≤1 |
Fe | 4-7 | 2-6 | ≤3 | ≤2 | ≤1.5 | ≤5 |
P | ≤0.04 | ≤0.02 | ≤0.04 | ≤0.04 | -- | ≤0.015 |
S | ≤0.03 | ≤0.02 | ≤0.03 | ≤0.03 | -- | ≤0.02 |
Si | ≤0.08 | ≤0.08 | ≤0.08 | ≤0.1 | ≤0.1 | ≤1 |
Ni | rest | rest | rest | rest | ≤65 | rest |
Co | ≤2.5 | ≤2.5 | ≤2 | ≤1 | ≤3 | ≤0.2 |
Ti+Cu | -- | -- | ≤0.7 | -- | ≤0.4 | ≤0.35 |
Al+Ti | -- | -- | -- | -- | ≤0.5 | ≤0.5 |
Cr | 14.5-16.5 | 20-22.5 | 14-18 | ≤1 | ≤1.5 | 6-8 |
Mo | 15-17 | 12.5-14.5 | 14-17 | 26-30 | ≤28.5 | 15-18 |
B | -- | -- | -- | -- | -- | ≤0.01 |
W | 3-4.5 | 2.5-3.5 | -- | -- | ≤3 | ≤0.5 |
V | ≤0.35 | ≤0.35 | -- | 0.2-0.4 | -- | ≤0.5 |
Alloy status | Tensile strength Rm N/mm² | Yield strength RP0.2 N/mm² | Elongation A5 % |
Solution treatment | 690 | 283 | 40 |
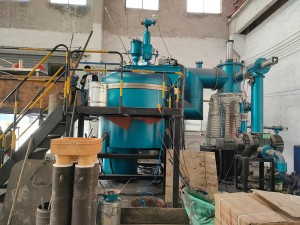
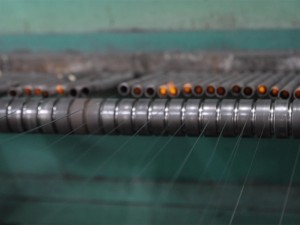
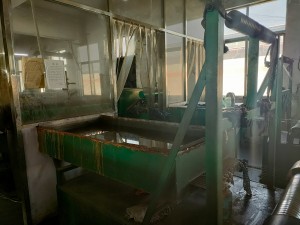
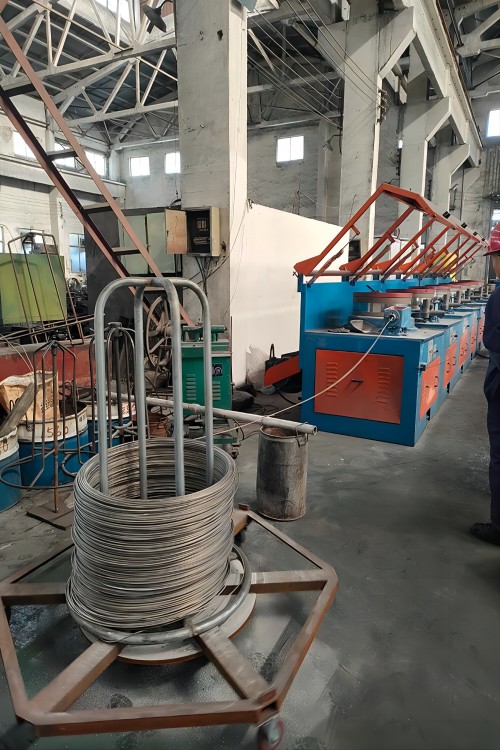
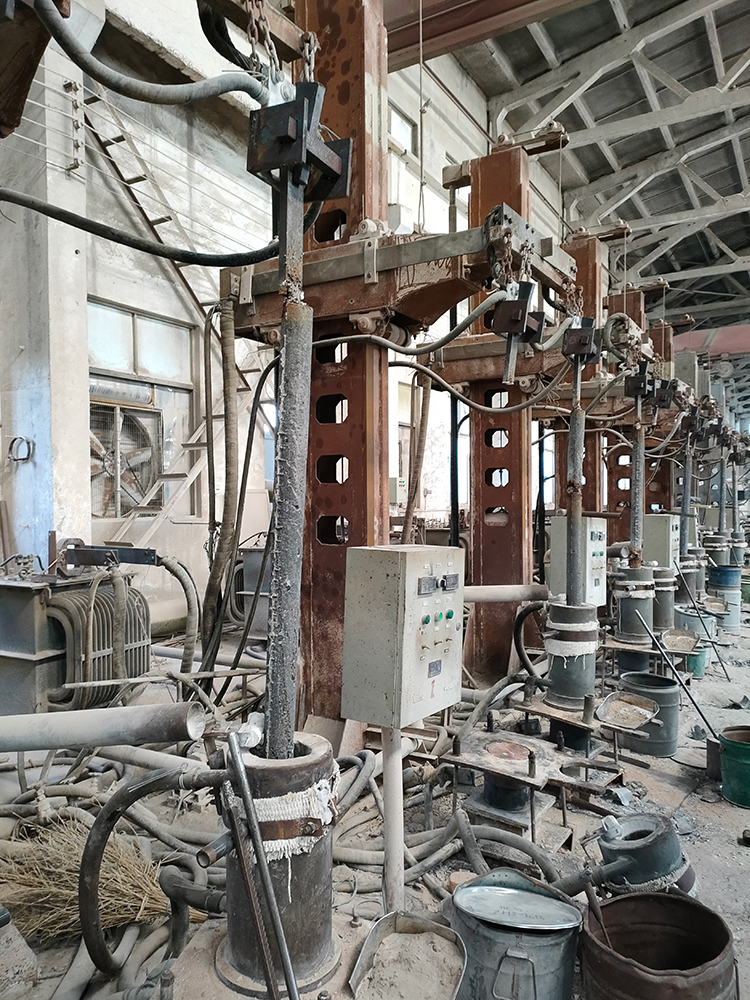
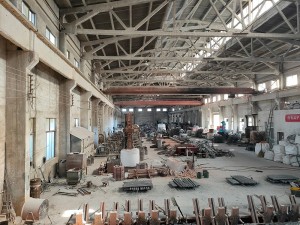
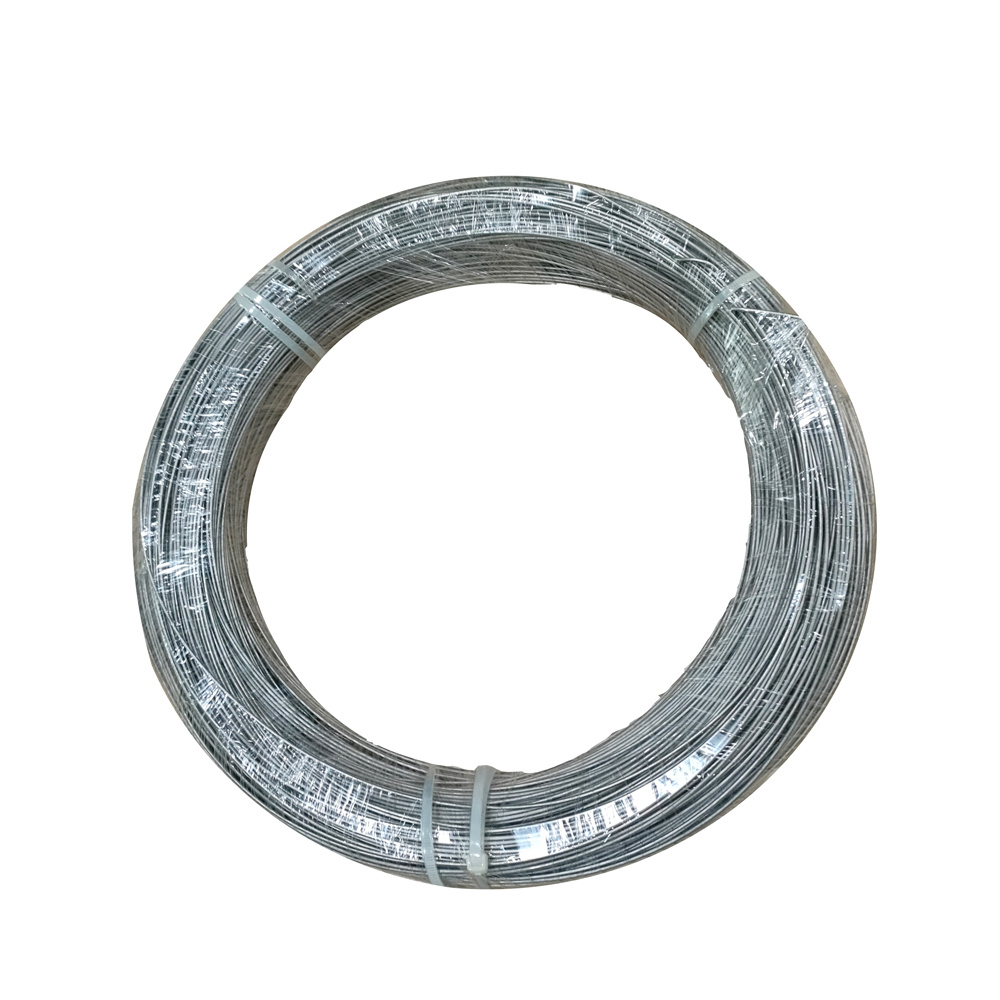
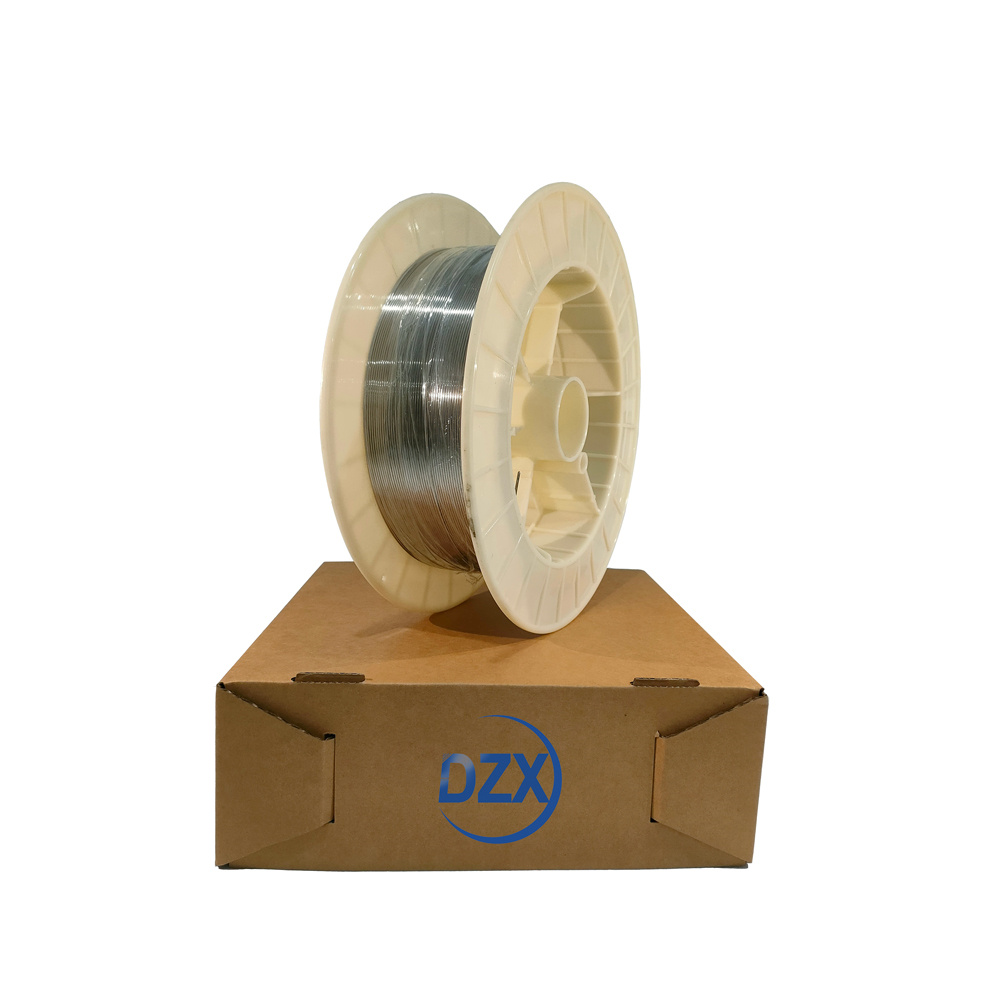
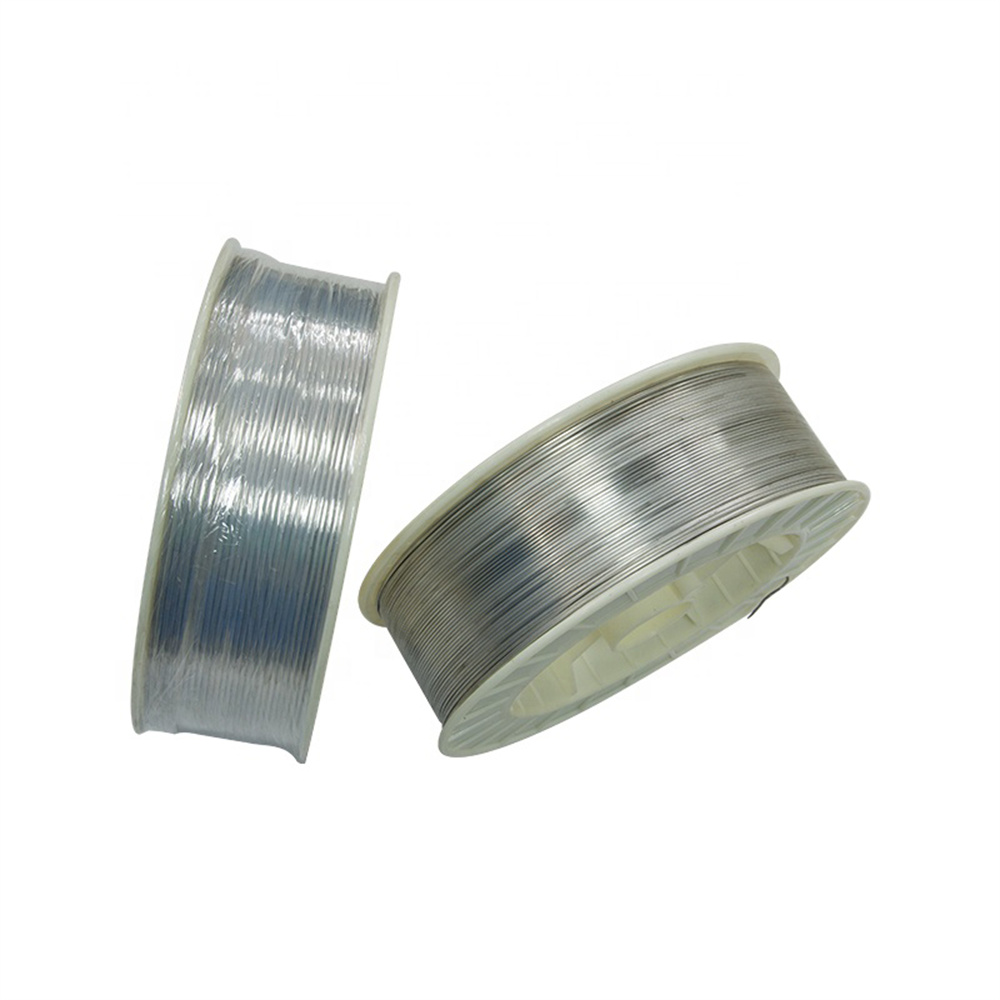